Coated aluminum coil refers to a product that is sprayed with color on the surface of the aluminum coil, also known asColor coated aluminum rollAnd colored aluminum rolls. The purpose of coating treatment is to have aesthetic effects in fields such as architecture, decoration, and home furnishings; The second is that the coating process and thickness are directly related to the product quality and service life of coated aluminum coils.
The coating process is a crucial step in the production of colored aluminum coils, which directly affects the coating quality and product durability. So the coating process is very strict. With the continuous improvement of coating equipment and the development and utilization of new coatings, the production of coated aluminum coils is becoming more mature, and processing costs are also decreasing. The development of coated aluminum coils is rapid. What is the specific process for coating aluminum coils?
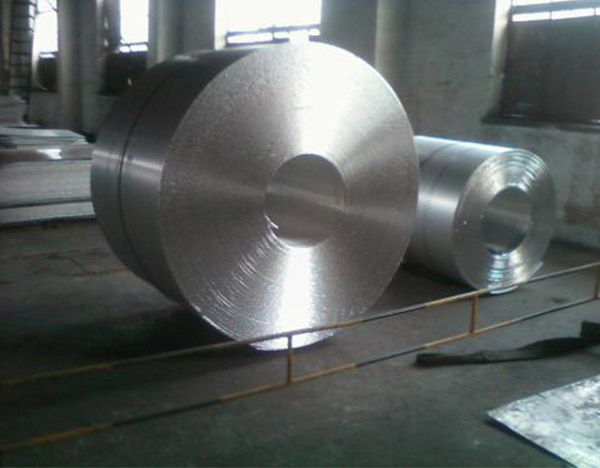
Generally speaking, the production process of coil coating consists of five steps, namely coil input, cleaning and chemical treatment, painting, curing, and finished product output. The process layout and equipment composition are different in different situations, but the basic parts are the same.
1. The raw material roll input is continuously uncoiled by the uncoiler, ensuring the continuous and stable input of the coil into the production line. Some use a cross rotating beam type winding machine, while others use two alternating front and rear uncoilers. In short, it is for timely submission of papers;
2. Surface cleaning and chemical treatment are used to clean the upper and lower surfaces of the aluminum coil, undergo chemical pre-treatment, and ensure that the paint adheres firmly;
3. Painting, a production line with at least two roller coating machines to ensure the color of the topcoat and primer;
4. It refers to the curing of the paint layer, which means that the newly painted coil should be fixed in front of the next roller to avoid mutual adhesion and damage. Generally, it includes at least two curing boxes;
5. It is the output of finished products, ensuring that the production line speed is synchronized with the transfer of finished rolls.