Aluminum exhaust pipe is mainly used in the refrigeration system of 10 ℃ to -45 ℃ cold storage, and is an evaporator used in various food freezing and refrigeration warehouses. The liquid inlet and outlet parts of the aluminum exhaust pipe use high-frequency resistance welding of copper aluminum joints. The aluminum pipe has a thickness of 2mm without any drop, and has a pressure resistance of 4.5Mpa. Cooling capacity of aluminum exhaust, K value ≈ 10W/(m2 · ℃) [average value], according to the design specifications of cold storage, Q=K · A· Δ t. The temperature difference taken during the actual mixing process Δ T=10 ℃. Considering the issue of frost formation in cold storage, the aluminum exhaust pipes in low-temperature storage are generally calculated based on a lower limit of 90W/M2 to prevent insufficient cooling capacity after frost formation. The high temperature storage without frost can be calculated based on the upper limit of 140W/m2.
Configuration of aluminum bars
Calculate equipment load to determine the heat exchange area of aluminum bars
Calculation of cooling equipment load: You can refer to relevant cold storage design manuals for detailed calculations. The formula is as follows
Qq= Q1 + PQ2+ Q3+ Q4
Qq - Cooling equipment load in the cold room, W;
Q1- Maintenance structure heat transfer, W;
Q2- Heat of goods, W;
Q3- Ventilation heat flow rate, W;
Q4- Operating heat flow rate, W;
P - Load factor. Take 1.3 for cooling room and freezing room P, and 1.0 for other cooling rooms;
By substituting the above formula into the known technical parameters, the load value of the cooling equipment in the cold storage can be obtained, which is the cooling capacity that the evaporator needs to provide. Large cold storage should strictly follow the above calculation process.
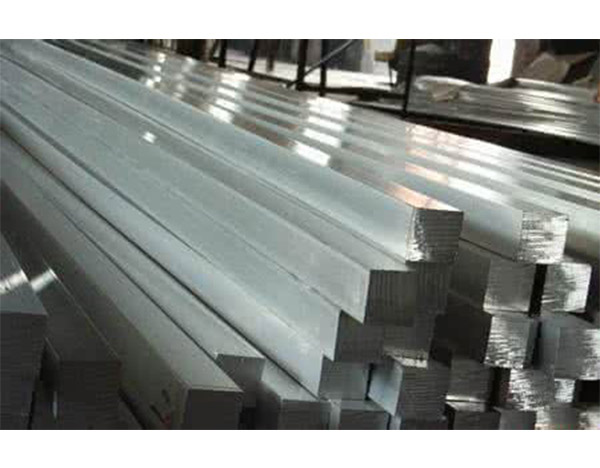